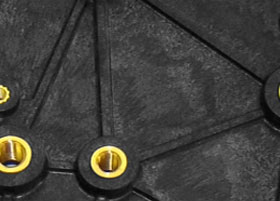
INSERT MOLDING
Insert molding involves molding plastic around a core or “insert”. Most often, the insert is a metal object, such as a pin, threaded rod, electrical contact, wire, etc. The insert could also be made out of another plastic or composite material—virtually anything that can withstand the heat and pressure of the molding process.
Insert molding is often used to join the insert and plastic together more securely than assembly allows. Moreover, it often eliminates post-molding assembly and saves the additional cost incurred in a secondary operation.
MIC is highly experienced with insert molding. We typically do this on our Vertical molding machines. The Vertical machines have an inherent advantage for insert molding—allowing the insert to be easily loaded into the mold, maintain a stable position during the molding cycle, and facilitate unloading the finished part after the molding cycle is complete. The insert is placed in the mold before the mold is closed and before raw material is injected. As the hot liquid plastic fills the mold and flows around the insert, it fills “undercut” features in the insert, such as holes, grooves, or bosses, thus securely captivating the insert into the finished part.